traffic control system ,CAST STUDY solution
Read the case gkten below and answer the questions giaen at the end
"Five years ago," confided Pqrnkaj Singhal, the 4S-year-old CEO of the automotive components manufacturer, Singhal Bosch Ltd. (a.k.a. SBL), to his guest, Taducha Ishikawa, the S0-year-old COO of the Indo-Japanese joint ventuqe, ABC Isami Ltd' (AIL), the leader in the domestic light commercial vehicles market, "we commissioned a training company, Dickens Inc., to introduce kaizen at our plant. As you know, we were born in 1985, in technical collaboration with the Munich-based Robert GMBH, to manufacture hydraulic and mechanical gears for the automobile industry, and so, had adopted its rigorous German management methods. But we felt the need for a system of continuous improvement in our manufacturing , processes five years on, which is why I thought of kaizen," l "Aftdr beginning with a flourish, what l am worried about is where our kaizen movement is . MS-96 4 taking us. For, the number of kaizens per man_year at the plant has' actually started falling 'in the last two years. From 1.57 in !gg0, the first year of its implementqtion, the kaizen rate per man-year. went up to tL.76 in 1993, but feil to 7.50 in 1995. Although this has nothing to do with the contract (for the supply of gears) we have signed,', he laughed shyly, "l was wondering if I could use this drive to Pune to tap your knowledge of the evolution of TQU programmes, in general and kaizen,inparticu|ar.Wheredoyouthinkwecou|d have gone wrong in implementing kaizen in our company ?" have gone wrong in implementing kaizen in our am a great believer kaizen," replied Ishikawa, quietly acknowledging the compliment, and settling down more comfortably in his corner of the car. "Contrary to what you sV, what is happening at SBL may be a good sign. Every company concentrates on quantity in the first few years, which is why the number of kaizens initially always shows an uptrend. Then, the focus shifts to quality although thd norms for what constitutes quality vary from company to company. But, invariably, the numbe r of kaizens falls, as a result, before it stabilises. That is quite normal- You are still on the right track..." "That is not our'problem," argued Singhal' "This decline has little to do with the quality of our kaiizens. I feel there are more fundamental issues... " Smiled Ishikawa : "You are in good company' Even corporations in the US and Europe have faced difficulties in implementing kaizen. Primarily, it is because they are so used to focussing on the results that they fail to recognise the importance of the processes that facilitate those results. Only when the top management conveys the message that the process is as important as the result are workers automatically encouraged to improve the way they work. And they are conditioned to look for ways by which to enhance their efficiency. That is what kaizen is all about. But, tell me; why did you.think of kaizen in the first place ?'l
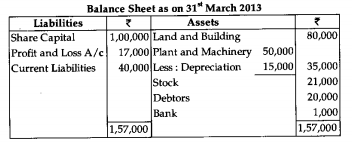
Singhal sighed, and shifted uncomfortably. "The early !990s were a difficult period," he explained. "With the automobile industry in a recession, our capacity utilisation fell to 40 per cent. There was a compelling need to lower our break-even point even as we introduced new types of gears, especially since there were competitive pressures on quality, prices, and delivery-schedules. Moreover, our raw material, energy, and labour costs were going up by 20 per cent a year. We had to find ways of reducing our costs and improving our productivity. That is why I decided to deploy kaizen..." "Forgive my saying so, but that approach was flawed," interrupted Ishikawa, uncharacteristically' "Kaizen is not a panacea for cost-reduction or productivity ' improvements. It is not a problem-solving tool : it only creates a mindset of improvement that equips people to address the ldrger issues better. What was your understanding of kaizen ?" . "l saw it as a way of constantly securing improvements everywhere by involving everyone in the company," said Singhal, after a thoughtful pause.
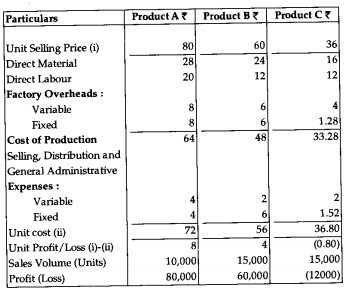
i'Fine. Then rryhy did you confine it to only your workers ?" asked Ishikawa immediatelv. "But that is what Dickens suggested," protested Singhal. "Kaizen was untested ground for me and I had to go by what the experts told us .... Also, we wanted results with which we could measure the success of the assignment. I must tell you that we linked their remuneration to cost-reduction. We said that our direct labour costs should come down to 8 per cent of our turnover over the next three years. Then, we structured their fees in such a way that 5O per cent was paid up-front, 30 per Qent on completion of training, and the rest was tied to the results the kaizen rnovement achieved..." 'lshikawa shook his head reproachfully. "In my experience, one way of ensuring the failure of kaizen is to link it to a business objective right at the ouiiet. That linkage, we in Japan believe, should be established later. In fact. kaizen works well only if it operates in a strategic vacuqm for the first two years. That period should be used by the CEO to create an atmosphere that will enable people to find new ways of lobking at issues, to get them to think in terms of what is good for the organisation, and to make it a habit to secure improvements, however marginal they may be, in the way they work. It is, of course, very different if you already have a progressive workforce..." Singhal admitted that SBL's 1,450-strong workforce wasn't particularly progressive although, with an average age of 27 years, they were quite receptive to new ideas and, initially at least, quite enthusiastic about kaizen.Ishikawa then asked how the consultants had gone about the training process. "Dickens spent the first six months training the workers. I addressed the inaugural session, where I spoke about why everyone should be constantly seeking little improvements every day in the way he, or she, works. And how we would always recognise.- and reward - those improvements." "Reward ? That's tricky," said Ishikawa, his eyebrows shooting up immediately. "Yes," winced Singhal. "But we realised it only as we went along, We came up with a flat monetary reward of Rs. 10 per kaizen. But Dickens suggested an in-built step-up mechanism, which appealed to me. So, the first t0 kaizens by a worker were rewarded at Rs. 10 each, the next tA kaizens by the same worker at Rs. 13 each, and the next lO kaizens at Rs. 15. each...' "You were after quick results," was all that Ishikawa would say, adding : "But this is like killing the goose that layi the golden eggs. Instead of seeking impror;ements out of their own free will, your employees would soon have begun chasing the money for its own sake. And there will be a spurt of enthusiasm initially but, sooner or later, the system will get reduced to a farce. That's why I said rewards aie a tricky issue. There is nothing wrong in offering a reward as long as you rnake sure that it is pegged to the stage at which the improvement has been effected. The greater the improvement, the lesser the reward. That is what we do in Japan..." "l don't quite. understand..." "Every problem, as we Japanese see it, has stages. Now, the gravity of the pqoblem increases progressively with each stage. Real improvement lies in dealing with a problem right at the initial stages. You will not see savings of a high order then because the problem has still not surfaced. Paradoxically, it is only when the problem becomes progressively more visible that the value of the improvements carry a progressively higher tag, and the savings so achieved appear more and more impressive. That is why, when you link monetary rewards inversely to the stages of a problem, you should pay more for an improvement that carries a lower price-tag and vice-versa." did not think of said a dazed "Our consultants did offer us a choice between payments in cash and payments in kind. We chose the former because it was easy to administer... Anyway, once the training sessions were over, we formed around 150 groups of between 8 and 10 workers each - of the same rank but from different departments - and suggested that they meet in the first week of every month. Each person was given upto six minutes to make a presentation on the improvements he had brought about at his workplace during the previous month. We did not want mere suggestions, but ideas that had be'en implemented into irnprovements. Each had to be presented in a separate A4-sized format with Before and After scenarios. It was a one-hour meeting, with a structured agenda, conducted by a senior manager, who was designated the Improvements Coordinator. Attendance at the meeting was optional since the idea was that there should not be any' external pressure to perform..." Ishikawa looked startled. "l was thinking about your coordinators. There is nothing wrong in confining kaizen to the workers. But, in that case, you should let the workers handle the meetings on their own too. Unlike in Japan, bringing in a manager is bound to create mistrust. I have always known that to happen in the Indian context..." "\,Ve did have problems there,','' said Singhal. "One worker actually asked me : what is the management's hidden agenda vis-a-vis kaizens ? At the same time, I didn't think there were any hard-and{ast rules we should go by. Honestly, are there any ?" "The crucial factor is the credibility of your message," replied Ishikawa, "and that can only come from consistency. What was your next step ?" . "All the" forms were displayed in a, central place we called the Kaizen Hall," continued Singhal. "Soon, there was little space left. So, we decided to let each employee display his kaizens in- his own workspace after they were signed off by the Improvement5 Coordinator. Two years into the eixercise, there was a huge increase in the number of kaizens, with over 90 per cent of our workers participating. But, as I told you earlier, :the enthusiasm about kaizen has waned. Nobody seems to be interested in it any more. In fact, I donrt think the spirit of continuous improvement that kaizen symbolises has percolated deep enough at SBL. Nor am I alone in my predicament; despite bringing in consultants, most companies have found it difficult to institutionalise kaizen. Evidently, the rewards system'has not been motivating enough. And if I dispense with it, what do I replace it with ?" "You should link it to perforrqance appraisal," said Ishikawa. o'But that should be part of the final stage. We believe that there are four sequential steps of kaizen implementation. First,'$et the quantity in kaizens. This is a churning stage, when all kinds of improvements are made, trivial and sound. Let positive energy be released in the .entire organisation, with everybody - from the CEO to the lowest worker - doing kaizens. This takes about two years for a company of your size. Second, shift. the focus to the quality of kaizens. This will happen on its own, with a cogent definition of wl'1at constitutes improvement automatically evolving. Third, link kaizens.to business goals." "How is that done ?" asked Singhal. . "Each kaizen form should list three of the company's business goals. Which could be, for example, customer satisfaction,. cogt reduction, and quality improvement. As the employee signs off the kaizen form,' he has to explicitl5r state how it has impacted on at least one of these three goals. This should be done, ideally, sometime during the fourth year. And the final stage is when kaizens are integrated with the performance appraisal process, wherein the number of kaizens generated by a worker during the year would be one of the criteria on which he is evaluated. That woulci institutionalise kaizen Of course, simultaneously, you should also develop support structures like a total quality movement in the company..." "Perhaps we have made too many, changes because we did not choose the right kaizen roadmap," said Singhal. "l am not sure how we can get back on the right track. Dickens has not billed us MS-96 1 5 for their last 20 per cent-of the fees, which i5 tied to the results we get. They too have suggested that we go in for a TQM roll-out, and we were planning to do so this year. Perhaps that will help us fine-tune ' the kaizen system. Meanwhile, ffiV direct labour costs shot up to L5 per cent last year. Thatr Vou say, is marginal to kaizen. But then, that leaves me even more worfied about the fate of our kaizen."
Questions : :
(i) Do you share the despondence of Singhal ? Has he done enough to ensure the success of SBL's Kaizen programme ? Has SBL. implemented the Kaizen programme in the right way ? How can improvement in the programme be elfected
(ii) Comment upon :
(a) The strategic aspects:of the reward system, and
(b) Participation of organisational members in the quality programme.